Technical Innovation in the Dehydration Treatment of Calcium Silicate Powder: An Advantage Analysis of Vertical Filter Presses and Filter Cloths
Release time:
2025-04-15
Application of Industrial Filter Cloth and Vertical Plate Filter Press in Hazardous Waste Residue Treatment—Taking Calcium Silicate Powder as an Example
In today's industrial production processes, the treatment of hazardous waste residue has become an important issue in environmental protection and resource recovery. Especially when dealing with solid waste materials such as calcium silicate powder, efficient solid-liquid separation equipment and suitable filter materials are crucial. The combination of vertical plate filter presses and industrial filter cloth provides an effective technical solution for the treatment of hazardous waste residue such as calcium silicate powder. This article will delve into the application and advantages of industrial filter cloth and vertical plate filter presses in hazardous waste residue treatment, particularly in calcium silicate powder treatment, analyzing their working principles, technical characteristics, and how to improve treatment effectiveness through optimized filter cloth selection.
I. Treatment of Hazardous Waste Residue and Characteristics of Calcium Silicate Powder
Hazardous waste residue, as the name suggests, refers to waste materials produced during industrial production that are harmful to the environment. Calcium silicate powder, as a typical hazardous waste residue, is widely found in various industrial production processes, especially in the manufacturing of calcium silicate materials, iron and steel smelting, and the chemical industry. The treatment of calcium silicate powder is quite difficult, mainly due to the following aspects:
Fine Particles, High Water Content Calcium silicate powder particles are usually small and have a high water content, often appearing as a slurry, which poses challenges for dehydration treatment.
Strong Viscosity Calcium silicate powder contains certain chemical components and has strong viscosity, making it easy to form filter cakes that adhere to the filter cloth during processing, resulting in difficulties in separation.
Complex Chemical Properties Calcium silicate powder may contain acidic, alkaline components or harmful substances, placing high demands on the corrosion resistance of equipment and filter materials.
To effectively address these challenges, it is particularly important to use appropriate solid-liquid separation equipment and filter cloth. Vertical plate filter presses, as highly efficient solid-liquid separation equipment, coupled with industrial filter cloth, provide a feasible solution for the dehydration treatment of calcium silicate powder.
II. Working Principle and Advantages of Vertical Plate Filter Press
A vertical plate filter press is a piece of equipment that uses pressure to separate solids and liquids; its working principle is relatively simple yet efficient. Its basic structure includes filter plates, filter cloth, a liquid discharge system, and a pressing system. During operation, the material to be treated (such as calcium silicate powder slurry) is fed into the filter press, and the filter cloth separates the material into solid and liquid parts. By applying pressure to the filter plates, the liquid part is squeezed out, forming a filter cake, and finally completing the solid-liquid separation.
Vertical plate filter presses have the following significant advantages:
Efficient Solid-Liquid Separation Vertical plate filter presses can provide high pressure, making the solid-liquid separation process more efficient, especially suitable for dewatering materials with high water content, such as calcium silicate powder.
Small Footprint Compared with traditional filtration equipment, vertical plate filter presses have a compact structure, suitable for sites with limited space, and can achieve large processing volumes in limited space.
Continuous Operation and High Automation Vertical plate filter presses support automated operation, reducing manual intervention and improving processing efficiency and safety.
Strong Adaptability Because the working principle of vertical plate filter presses is flexible, they can adapt to the treatment of different types of waste materials, especially materials such as calcium silicate powder that have fine particles and strong viscosity.
Although vertical plate filter presses have so many advantages, the effectiveness of their treatment largely depends on the selection and matching of the filter cloth.
III. The Importance of Industrial Filter Cloth in Calcium Silicate Powder Dehydration Treatment
In vertical plate filter presses, industrial filter cloth is a crucial component. The quality and performance of the filter cloth directly affect the efficiency of solid-liquid separation and determine the quality of the final filter cake and the cleanliness of the liquid. Especially for hazardous waste residues such as calcium silicate powder, which have viscosity and fine particles, selecting the appropriate filter cloth is crucial.
Filtration Accuracy The particles of calcium silicate powder are usually fine, and particles smaller than 1 micron require high accuracy of the filter cloth. The pore structure of the filter cloth must be able to effectively block these fine particles, ensuring that solid substances can be effectively retained while the liquid can flow out smoothly.
Abrasion Resistance and Tensile Strength During high-pressure dehydration, the filter cloth needs to withstand pressure from the filter press, especially when processing calcium silicate powder with strong viscosity, the filter cloth is easily subjected to wear and tear and stretching. Therefore, the filter cloth needs to have strong wear resistance and tensile strength to extend its service life.
Corrosion Resistance The process of treating calcium silicate powder may involve the presence of some acidic, alkaline, or other chemical components, requiring the filter cloth to have good chemical corrosion resistance to prevent damage or performance degradation due to chemical reactions.
Filter Cake Release Performance Because calcium silicate powder has strong viscosity, the filter cake is easily attached to the filter cloth, causing filter cloth blockage. High-quality filter cloth not only needs to have good filtration performance but also good filter cake release performance for subsequent operation and equipment cleaning.
Common filter cloth materials used for calcium silicate powder treatment include polyester, polypropylene, and polyamide. These materials have strong wear resistance, tensile strength, and good chemical resistance, meeting the various requirements for filter cloth in the calcium silicate powder dehydration process.
IV. Filter Cloth Selection and Optimization Schemes
For the special hazardous waste residue of calcium silicate powder, the selection of suitable filter cloth not only needs to meet the basic technical requirements but also needs to be optimized according to different processing technologies. Here are some common filter cloth selection schemes:
Monofilament Filter Cloth Monofilament filter cloth has high filtration accuracy and can effectively block fine particles, suitable for the treatment of materials such as calcium silicate powder. The pore structure of this filter cloth is uniform, providing good solid-liquid separation.
Composite Filter Cloth Composite filter cloths are usually made up of multiple layers of materials, combining the advantages of different layers. For example, the outer layer uses wear-resistant materials, while the inner layer uses materials with high filtration precision. This type of filter cloth is particularly suitable for handling highly viscous waste materials and can effectively improve the release performance of the filter cake.
Polyester/polypropylene filter cloth These materials have strong chemical corrosion resistance and can resist damage to the filter cloth from acidic and alkaline substances. They are suitable for the special chemical environment in the silicon calcium powder processing process.
Corrosion-resistant coated filter cloth For corrosive substances that may be present in silicon calcium powder, filter cloths with a corrosion-resistant coating can be selected to extend their service life.
By reasonably selecting the filter cloth, not only can the dewatering efficiency of silicon calcium powder be improved, but also the service life of the equipment can be extended, and the maintenance cost can be reduced.
V. Analysis of Actual Application Cases
In some industrial enterprises, the combination of vertical filter presses and industrial filter cloths has already achieved remarkable results in the processing of silicon calcium powder. For example, a certain steel plant has successfully improved the dewatering efficiency of silicon calcium powder by introducing a solution combining vertical filter presses and customized filter cloths. By using monofilament polyester filter cloths, these enterprises can effectively reduce energy consumption, improve dewatering effect, and reduce equipment cleaning time during the processing process.
VI. Summary
The combination of industrial filter cloths and vertical filter presses provides strong support for the treatment of hazardous waste residues such as silicon calcium powder. The filter cloth plays a decisive role in the dewatering process, and its performance directly affects the processing efficiency and cost. By reasonably selecting and optimizing the filter cloth, the dewatering effect of silicon calcium powder can be improved, equipment failures can be reduced, and overall production efficiency can be improved. In the future, with the continuous advancement of technology, the combination of vertical filter presses and industrial filter cloths will play an even greater role in more fields, providing more efficient and environmentally friendly solutions for the treatment of industrial waste.
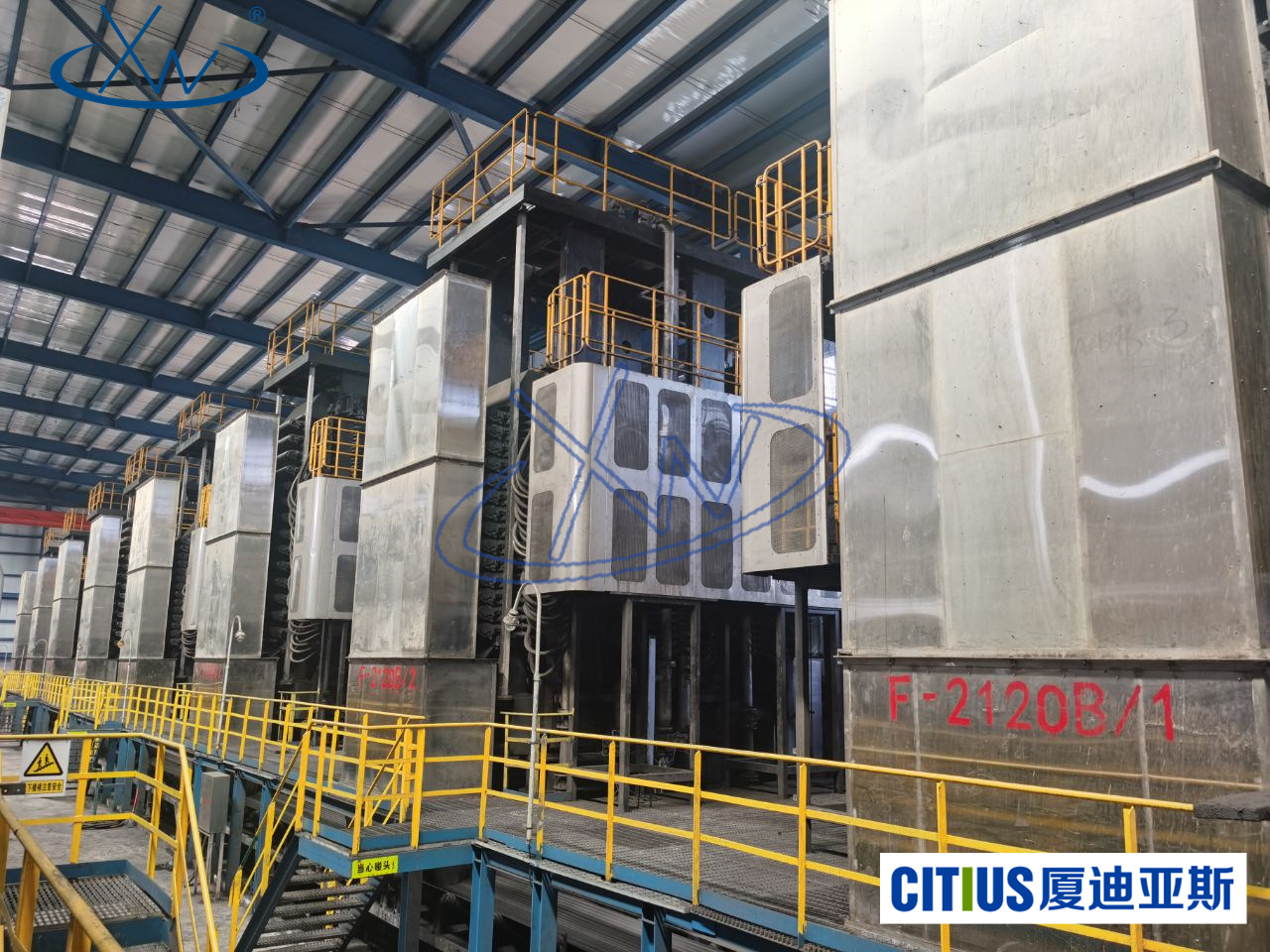
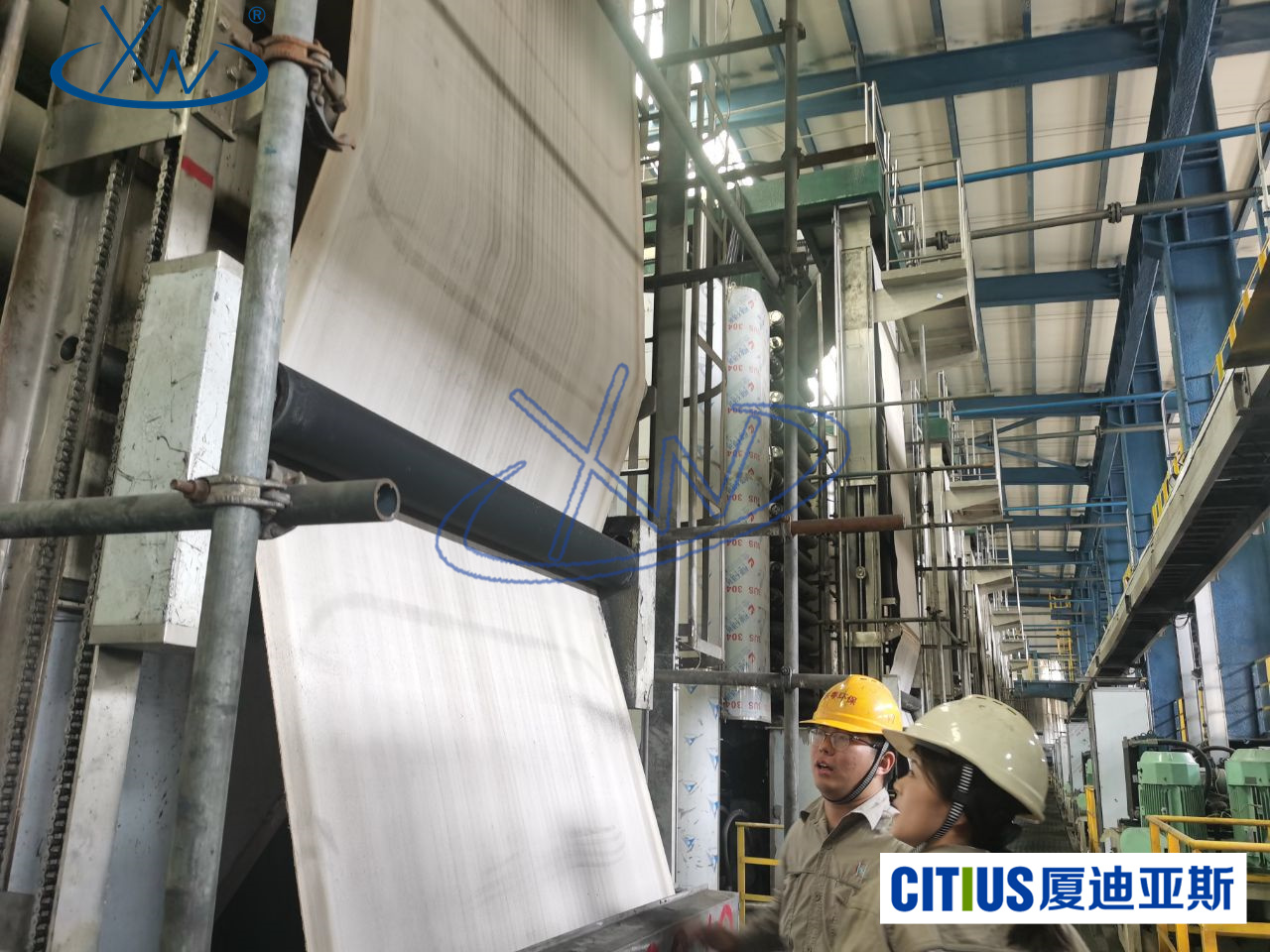
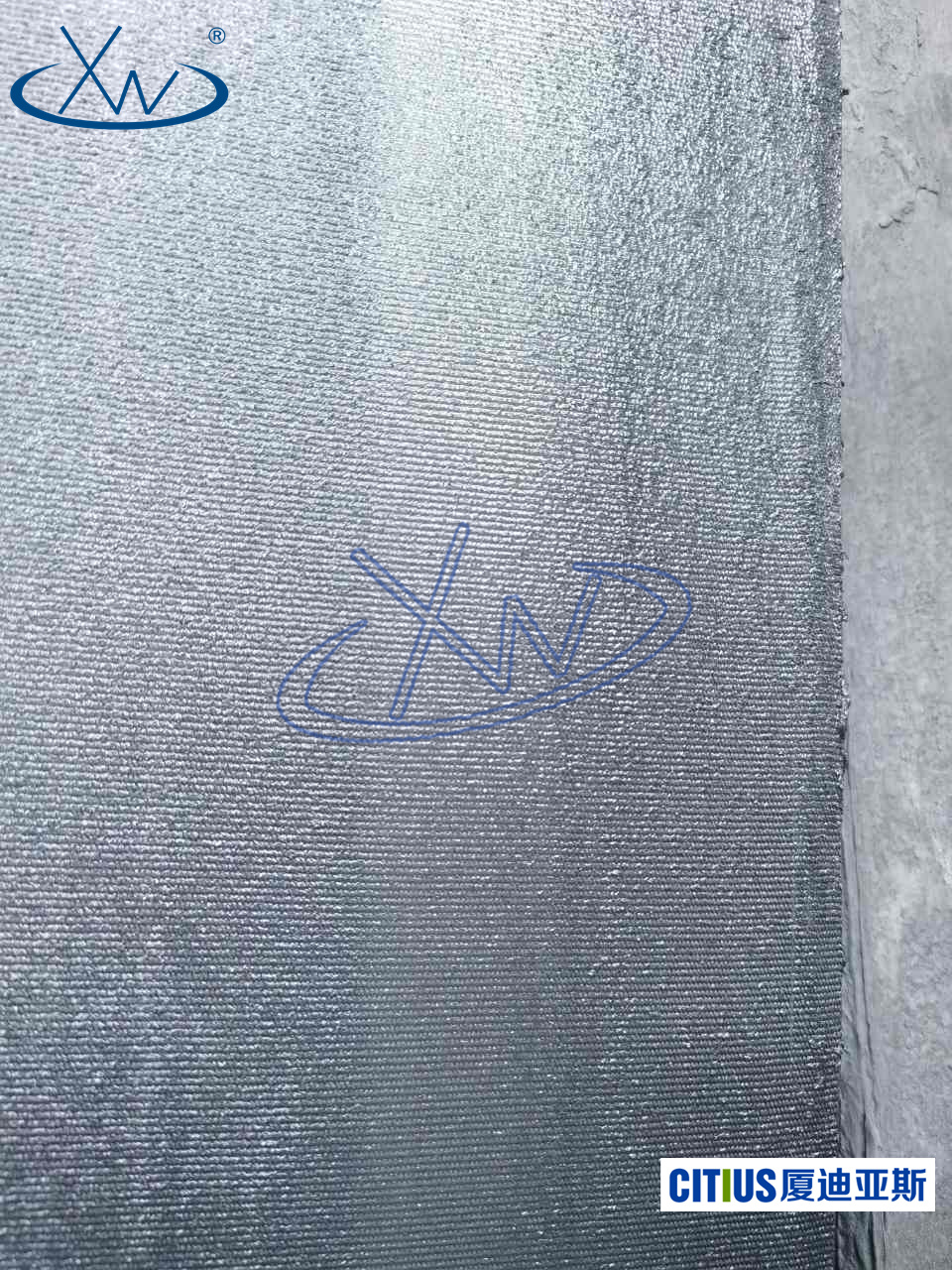
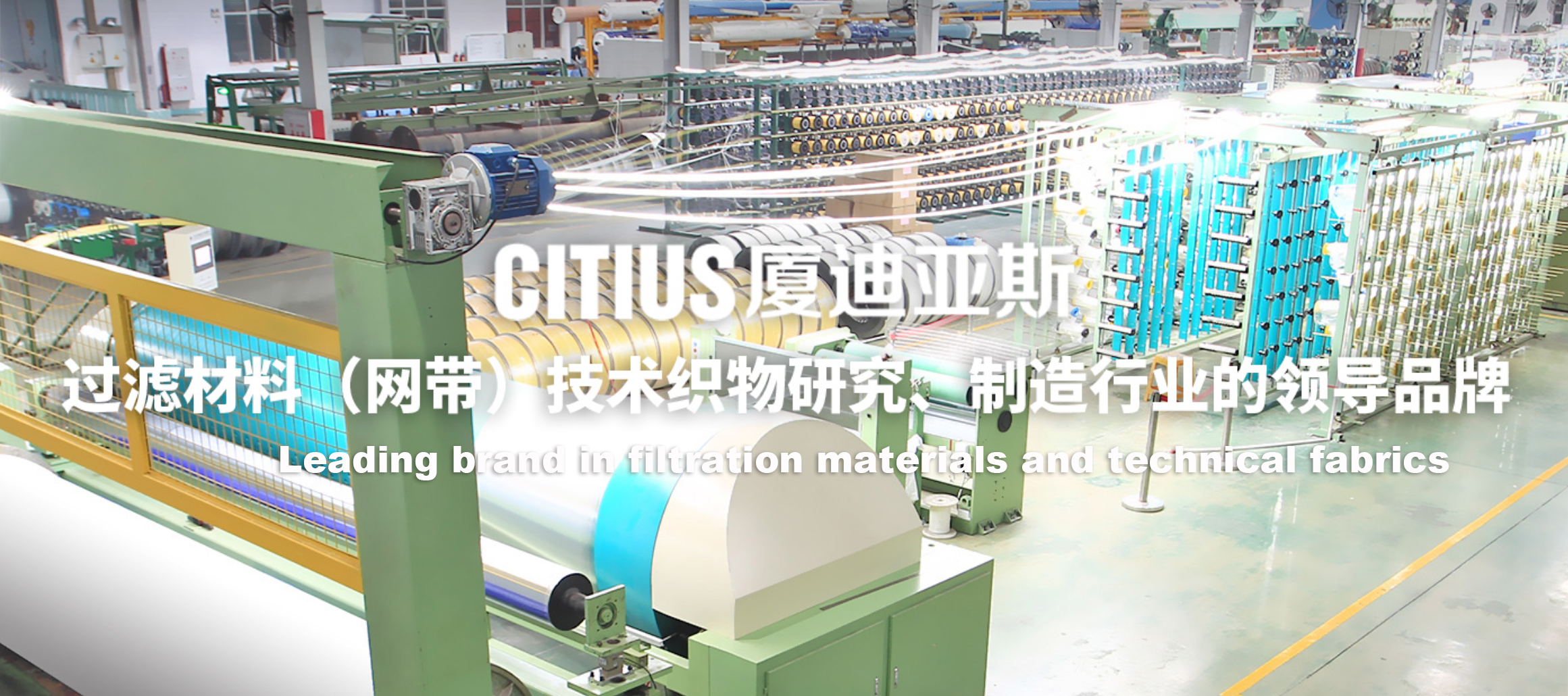