








Industrial filter cloth, vertical filter press, hazardous waste residue treatment silicon calcium powder
Share to
Detailed Description
- Industrial filter cloth, vertical plate filter press, hazardous waste residue treatment calcium silicate powder
Filter press type: Vertical plate filter press
Application industry: Hazardous waste residue treatment
Material description: Calcium silicate powder
Filter cloth Model: 012, 014
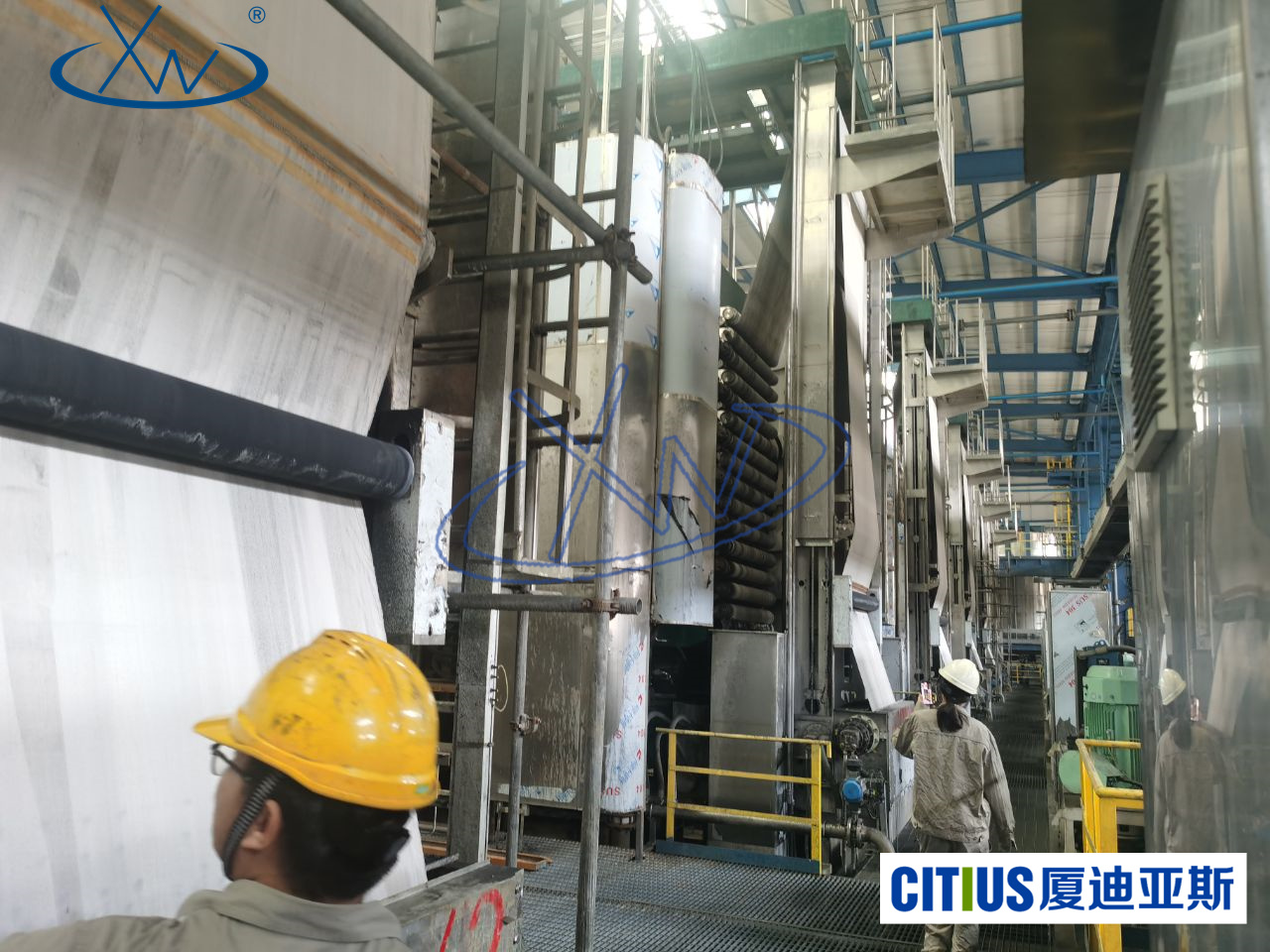
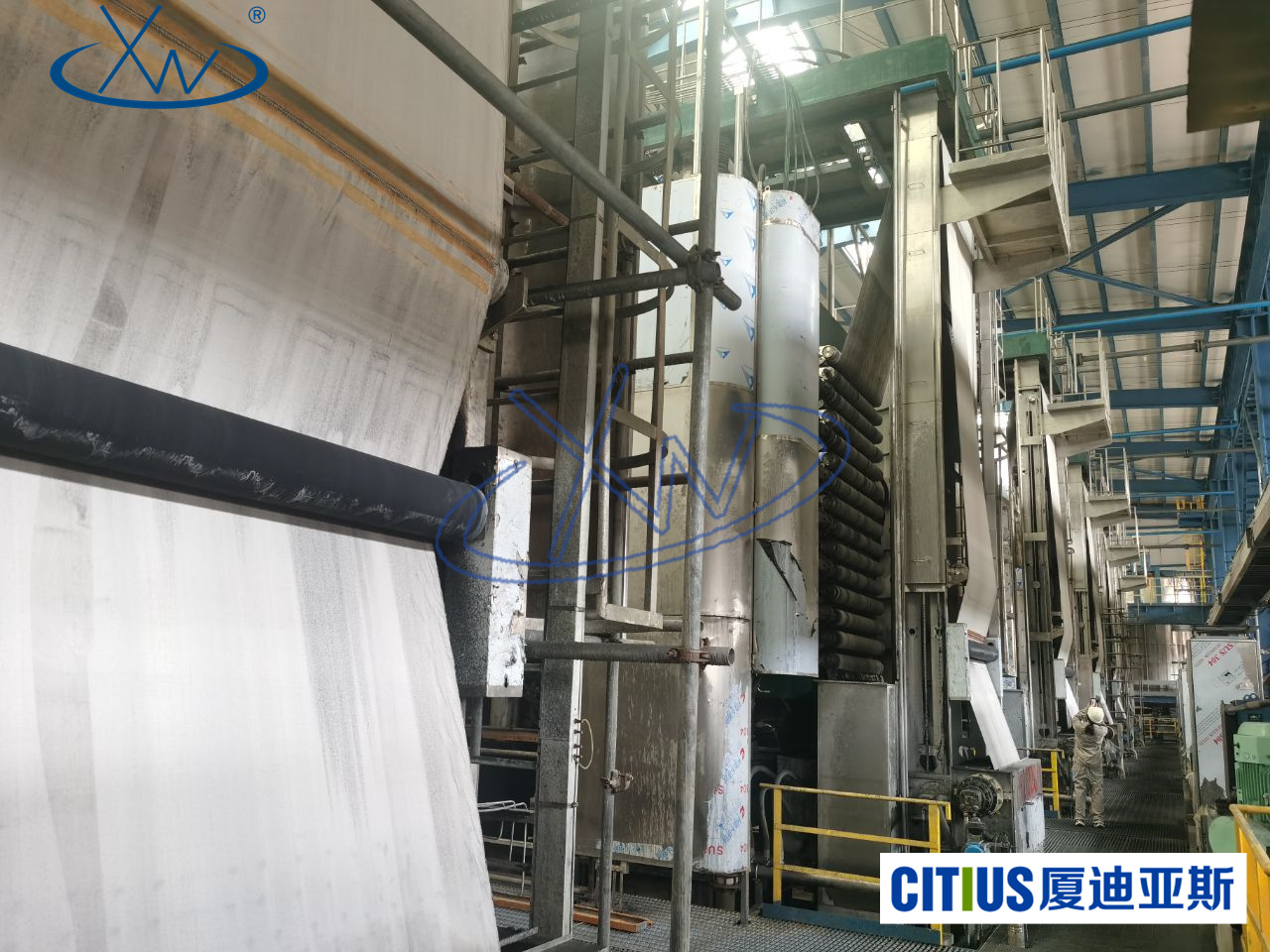
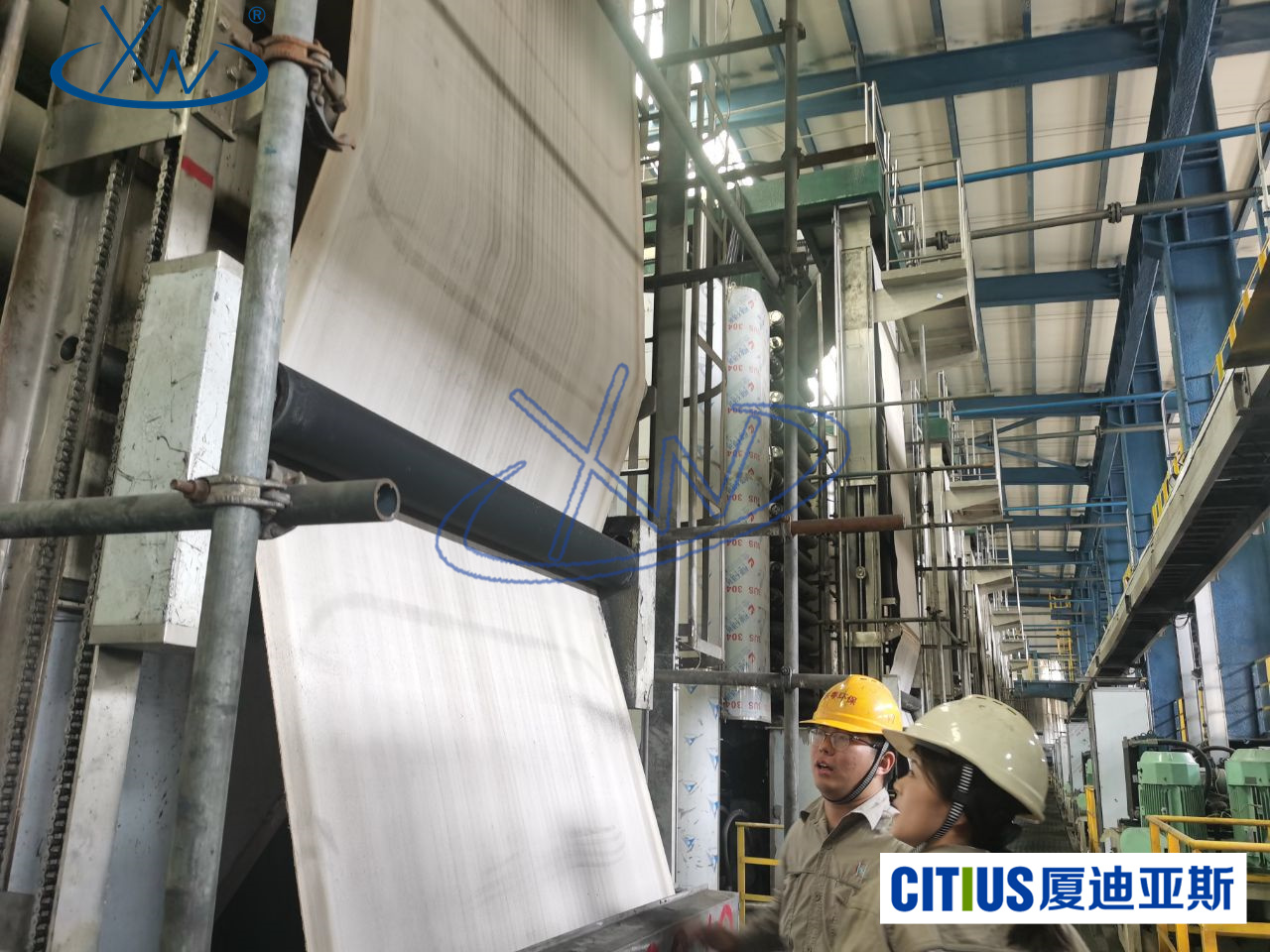
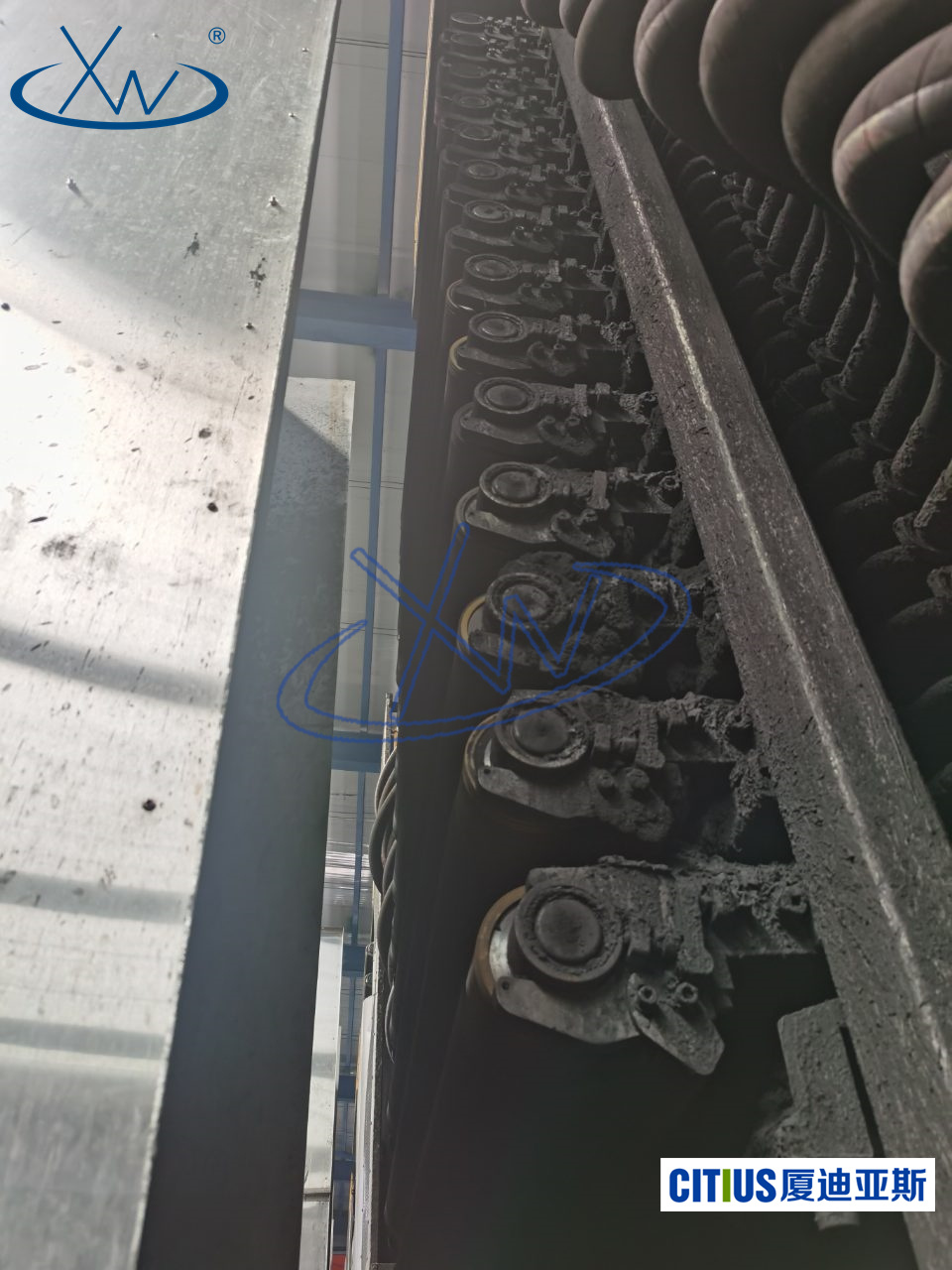
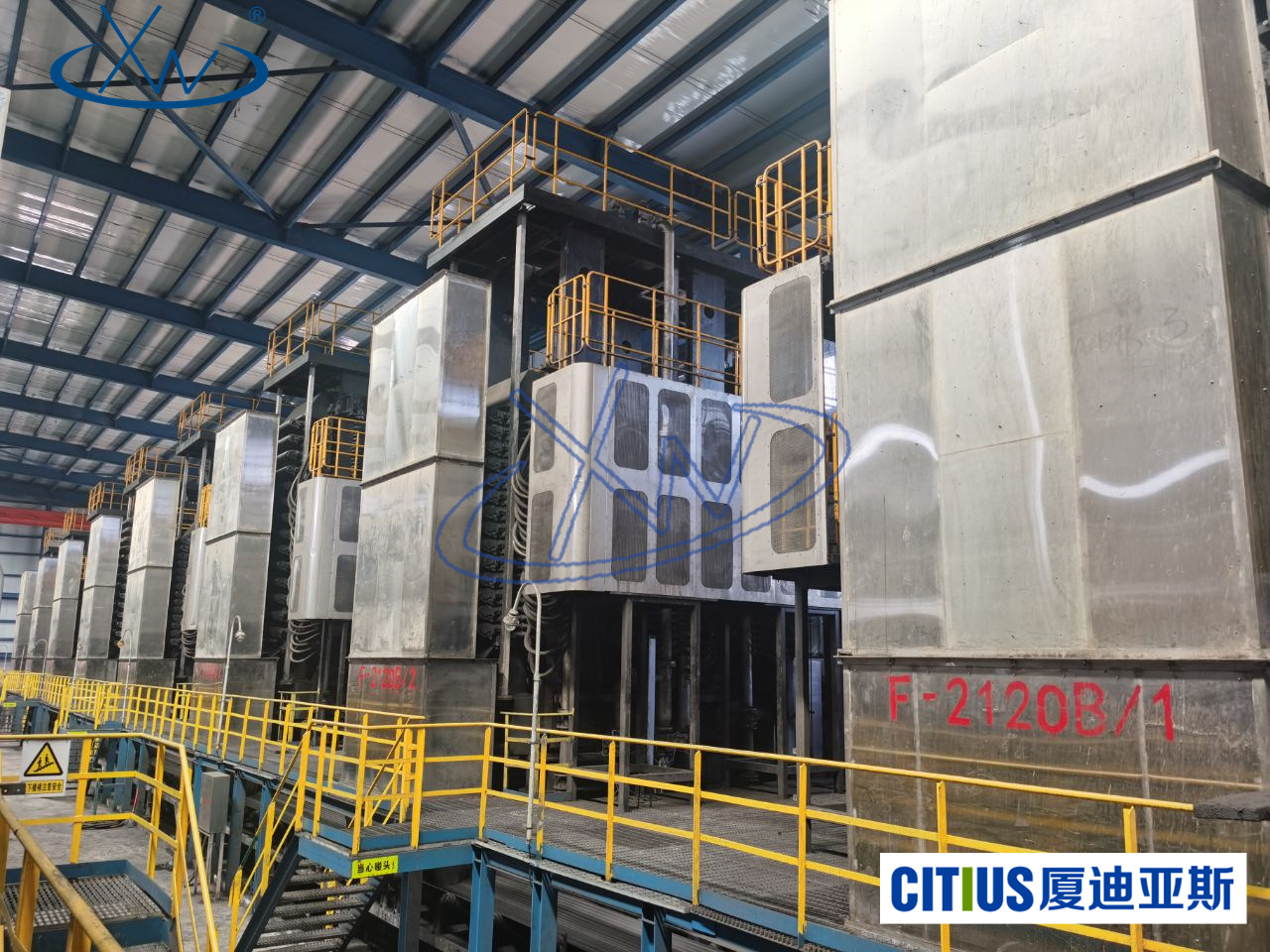
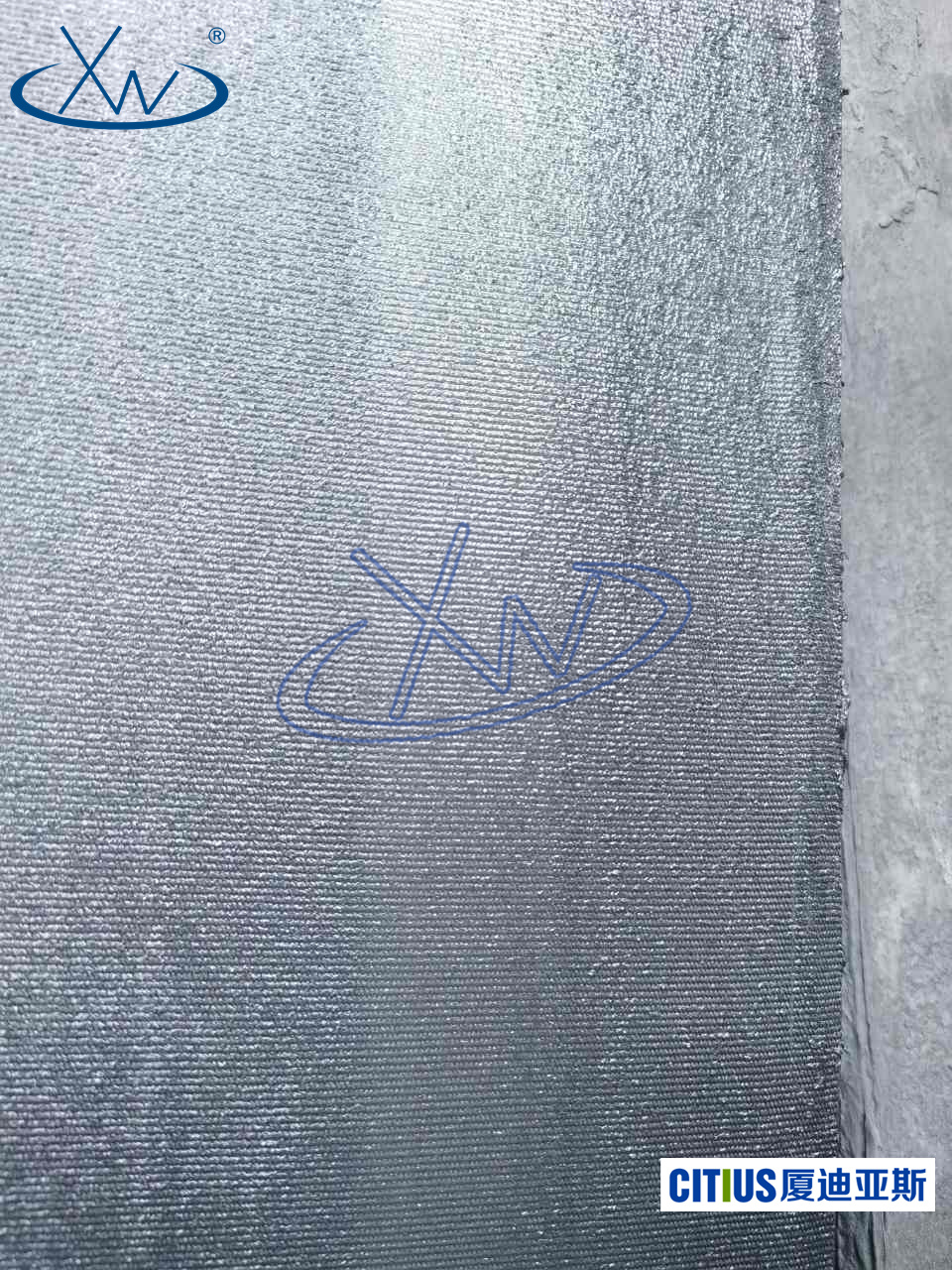
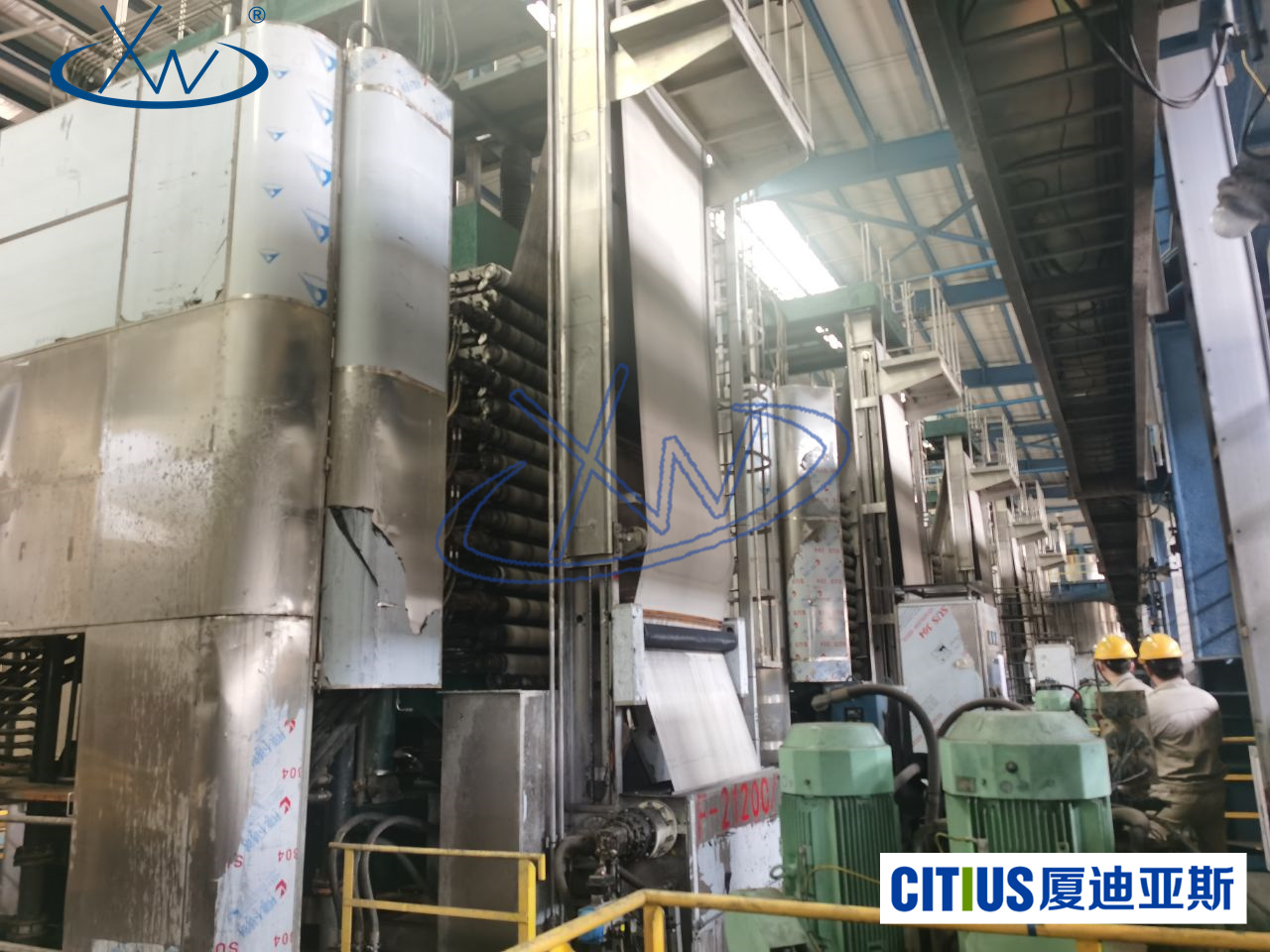
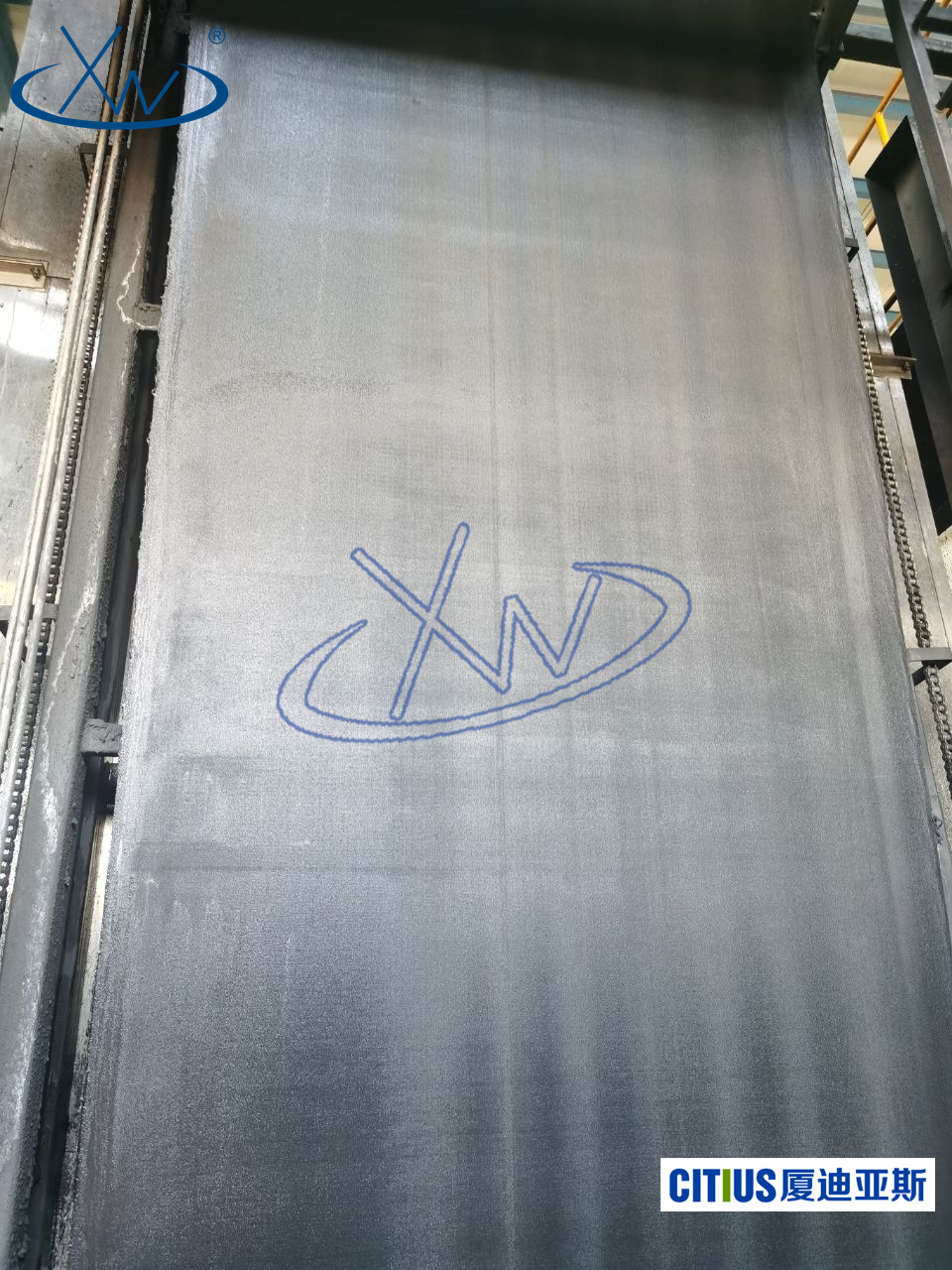
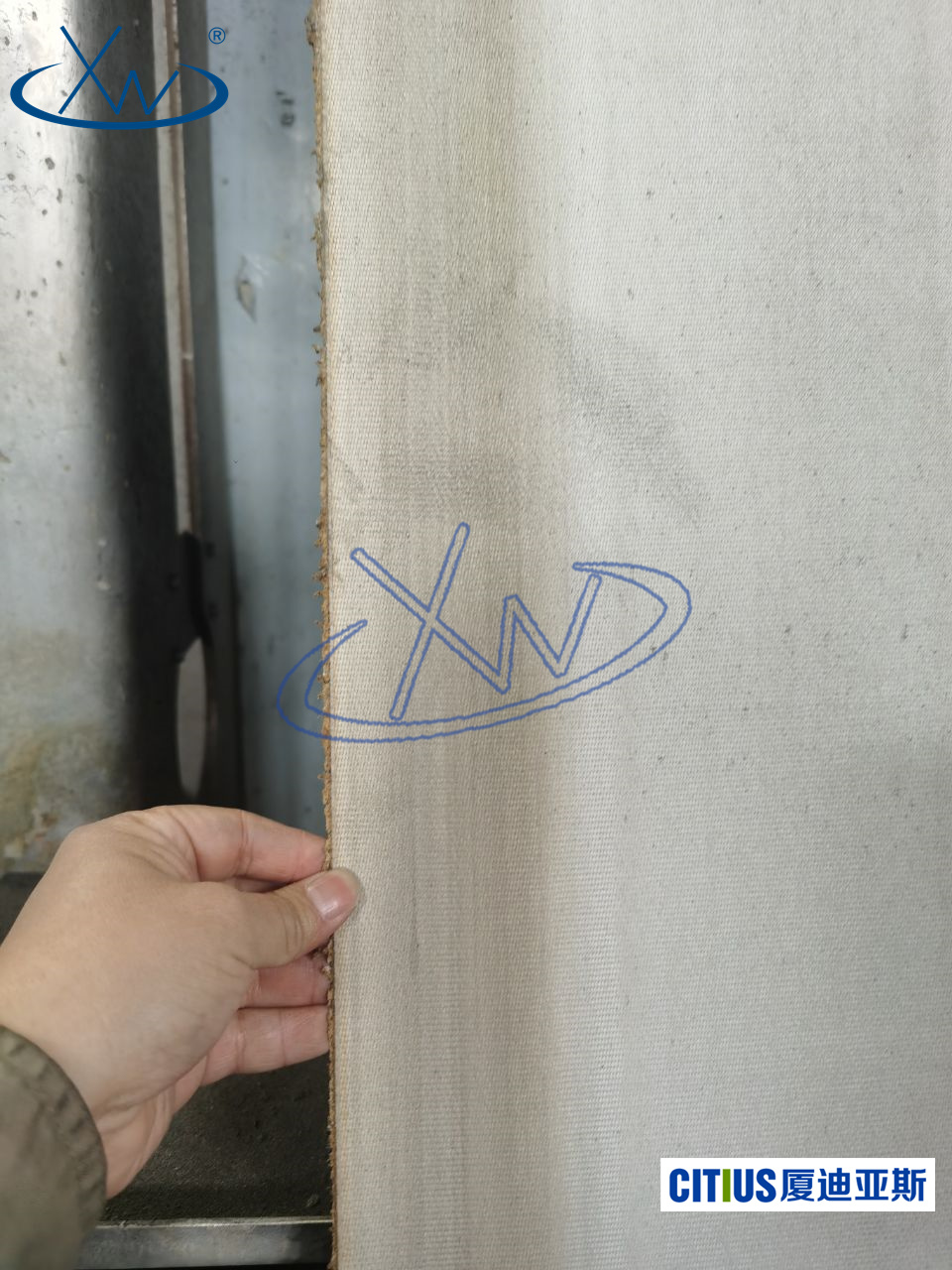
In the process of hazardous waste residue treatment, especially when dealing with solid waste such as calcium silicate powder, the application of industrial filter cloth is crucial. The vertical plate filter press, as a highly efficient solid-liquid separation equipment, is widely used in the dehydration and treatment of calcium silicate powder. The following are the roles and key advantages of industrial filter cloth in vertical plate filter presses for the treatment of hazardous waste residue (such as calcium silicate powder):
1. Challenges in Hazardous Waste Residue Treatment
Hazardous waste residue, such as calcium silicate powder, is a solid waste generated during industrial production, usually containing a large amount of water. The particles of calcium silicate powder are relatively small, and sometimes contain certain harmful substances, so efficient filtration and dehydration processes are required during processing. The dehydration treatment of calcium silicate powder faces the following challenges:
- High water content Calcium silicate powder usually has a high water content, requiring the filter cloth to have good filtration efficiency and dehydration performance.
- Small and sticky particles Small particles and highly viscous substances may cause filter cloth clogging and difficulty in filter cake removal.
- Special chemical properties Calcium silicate powder may contain certain chemical components, which requires the filter cloth to have strong corrosion resistance.
2. Advantages of Vertical Plate Filter Press
Vertical plate filter presses utilize their unique structure and powerful pressing capabilities to efficiently perform solid-liquid separation, especially suitable for processing hazardous waste residue and materials with high solid content. Its working principle is to apply pressure to the filter plates to squeeze the liquid out of the solid material, forming a filter cake, and finally discharging it. The advantages of vertical plate filter presses include:
- High-pressure dehydration By applying higher pressure, the water in the hazardous waste residue can be effectively removed, especially for calcium silicate powder with high water content, significantly improving dehydration efficiency.
- Strong adaptability Vertical plate filter presses have a large filtration area and can adapt to various types of waste materials, including fine particles and highly viscous materials.
- Energy-efficient and efficient Compared with other filtration equipment, vertical plate filter presses have higher energy utilization efficiency when processing hazardous waste residue, and can achieve a continuous and efficient processing process.
3. The Key Role of Industrial Filter Cloth in Calcium Silicate Powder Treatment
In vertical plate filter presses, the filter cloth is a key factor determining the filtration effect and efficiency. The treatment of calcium silicate powder requires the filter cloth to have the following characteristics:
- High filtration accuracy Because the particles of calcium silicate powder are very fine, it is crucial to choose a filter cloth with appropriate porosity and high filtration accuracy. Commonly used filter cloth materials include polyester, polypropylene, and nylon.
- Abrasion resistance and tensile strength Under high pressure, the filter cloth needs to have sufficient abrasion resistance and tensile strength to cope with long-term operation and pressure impact.
- Corrosion resistance If the calcium silicate powder contains certain chemical components (such as acidic or alkaline substances), the filter cloth must have strong corrosion resistance to ensure that it is not damaged or affects the filtration effect during the entire processing process.
- Good filter cake release performance Due to its characteristics, calcium silicate powder may make the filter cake relatively firm, so it is necessary to choose a filter cloth that can help to quickly remove the filter cake to avoid clogging and reduce production efficiency.
4. Filter Cloth Selection and Application
Generally, the following types of industrial filter cloths are recommended for calcium silicate powder treatment:
- Monofilament filter cloth It has high filtration accuracy and good pressure resistance, suitable for processing fine particulate materials.
- Polyester / Polypropylene filter cloth These two types of filter cloths have good chemical corrosion resistance and can effectively cope with the chemical components in calcium silicate powder.
- Composite filter cloth In some cases, composite filter cloths have better wear resistance and dehydration performance, and can provide stronger filtration efficiency during processing.
5. Summary
Vertical plate filter presses combined with suitable industrial filter cloths can effectively treat calcium silicate powder in hazardous waste residue. In the dehydration process, the choice of filter cloth determines the quality of the treatment. High-quality filter cloths can improve solid-liquid separation efficiency, ensure efficient dehydration of calcium silicate powder, and reduce the difficulty of filter cake removal. For hazardous waste residue treatment, the correct filter cloth selection and reasonable operation procedures will ensure efficient resource utilization and sustainable environmental development.
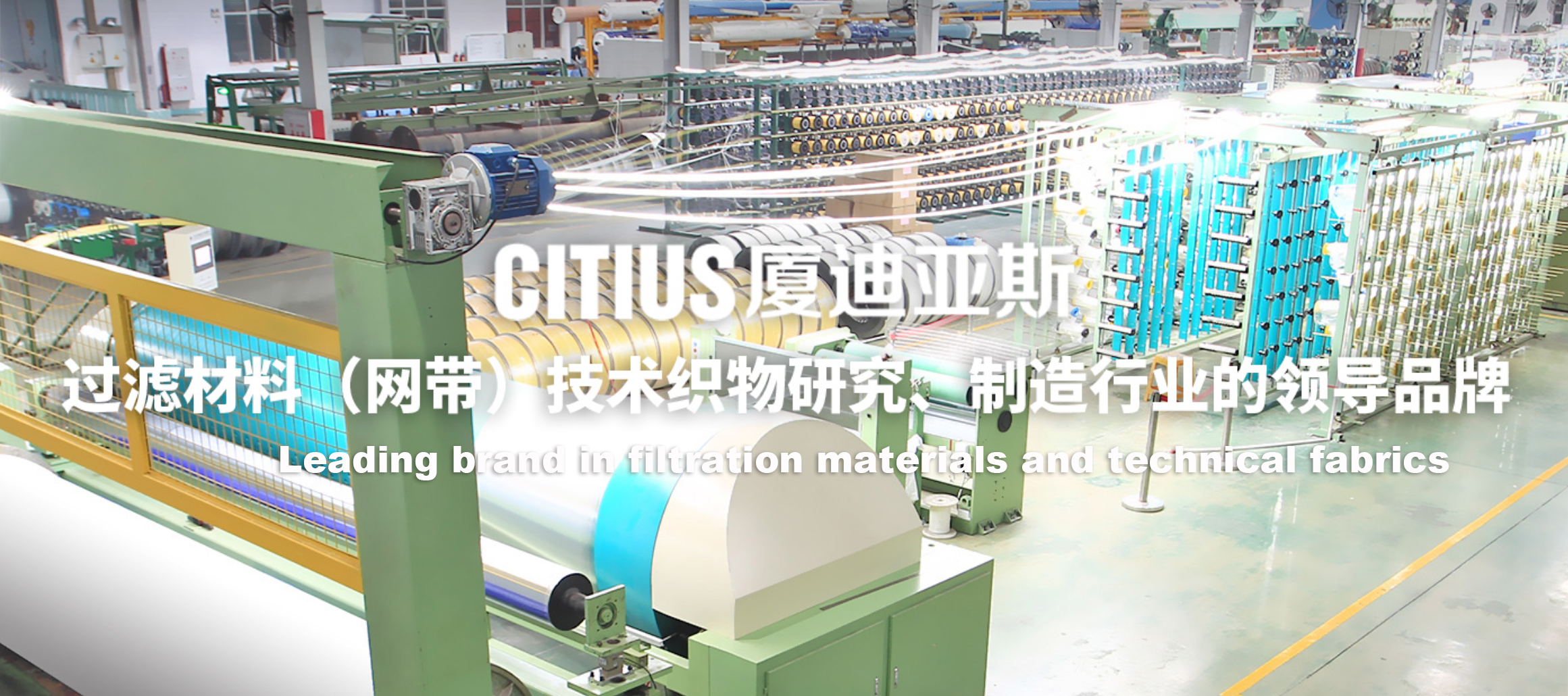